The absence of brushes eliminates friction and adds to its service life, while higher efficiency and less maintenance translate into lower costs. Brushless motors have higher power, are more precise, and are more reliable for their size, compared with brushed motors, and are thus preferred for topmost performance and durability applications.
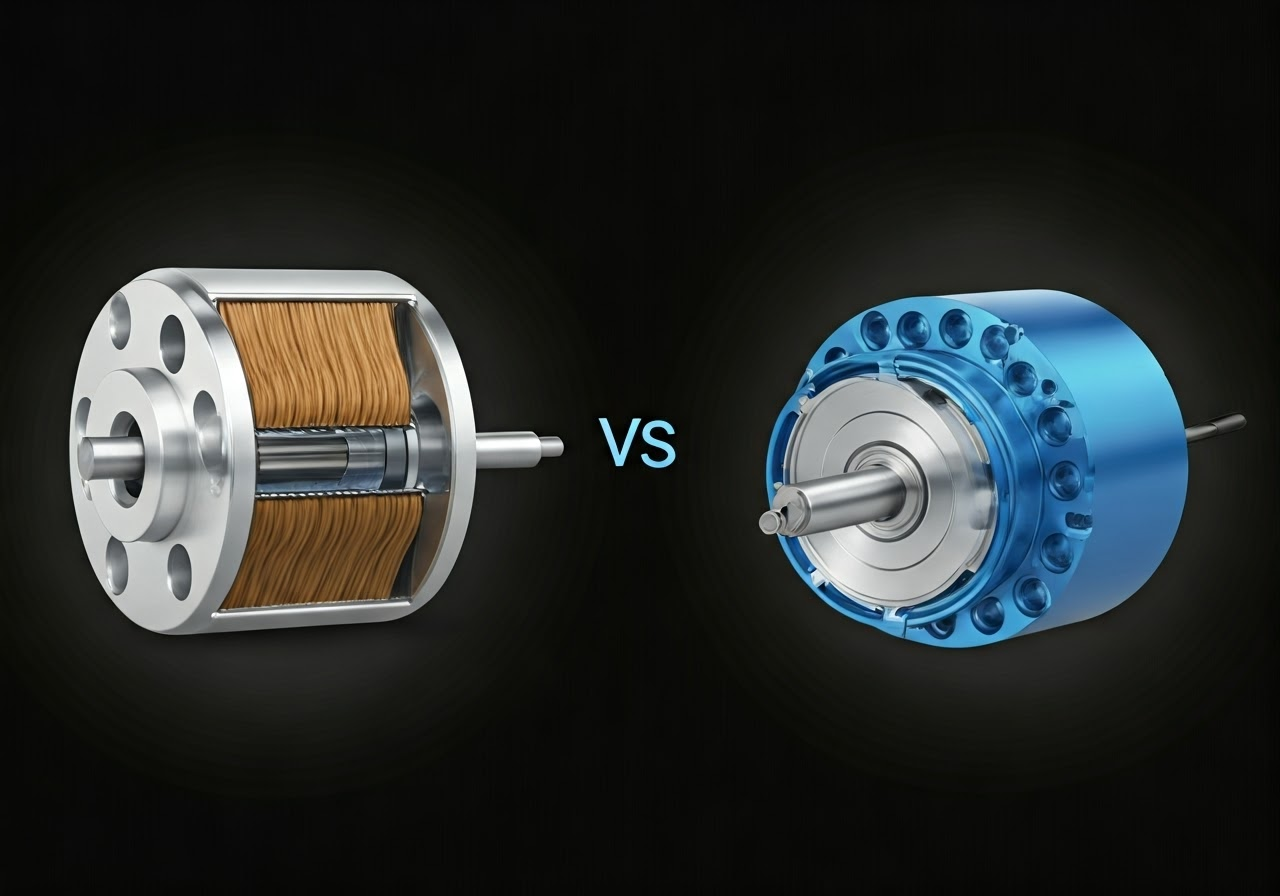
Key Highlights
- Brushed and brushless motors are used in many applications. They work based on magnetic interaction. However, they are built differently and use different communication methods.
- Brushed motors are cheaper and simpler. They use brushes and a commutator for commutation. This causes friction, wear, and noise.
- Brushless motors have electronic commutation. This means no physical contact is needed. They are more efficient, last longer, and are quieter.
- Choosing the right type of motor depends on things like speed, torque, precision, maintenance needs, and cost.
- It is important to know the advantages and disadvantages of the different motor technologies. This helps you make smart choices based on what you need for your specific application.
Introduction
Electric motors are very important for many devices and systems we use every day. They change electrical energy into mechanical work by using magnetic fields. The key to these motors is their ability to create rotational motion. This happens by using the pull and push forces between permanent magnets and electromagnets. This complex interaction between magnets allows for many uses, from basic toys to advanced machines in industries.
Understanding Brushed Motors
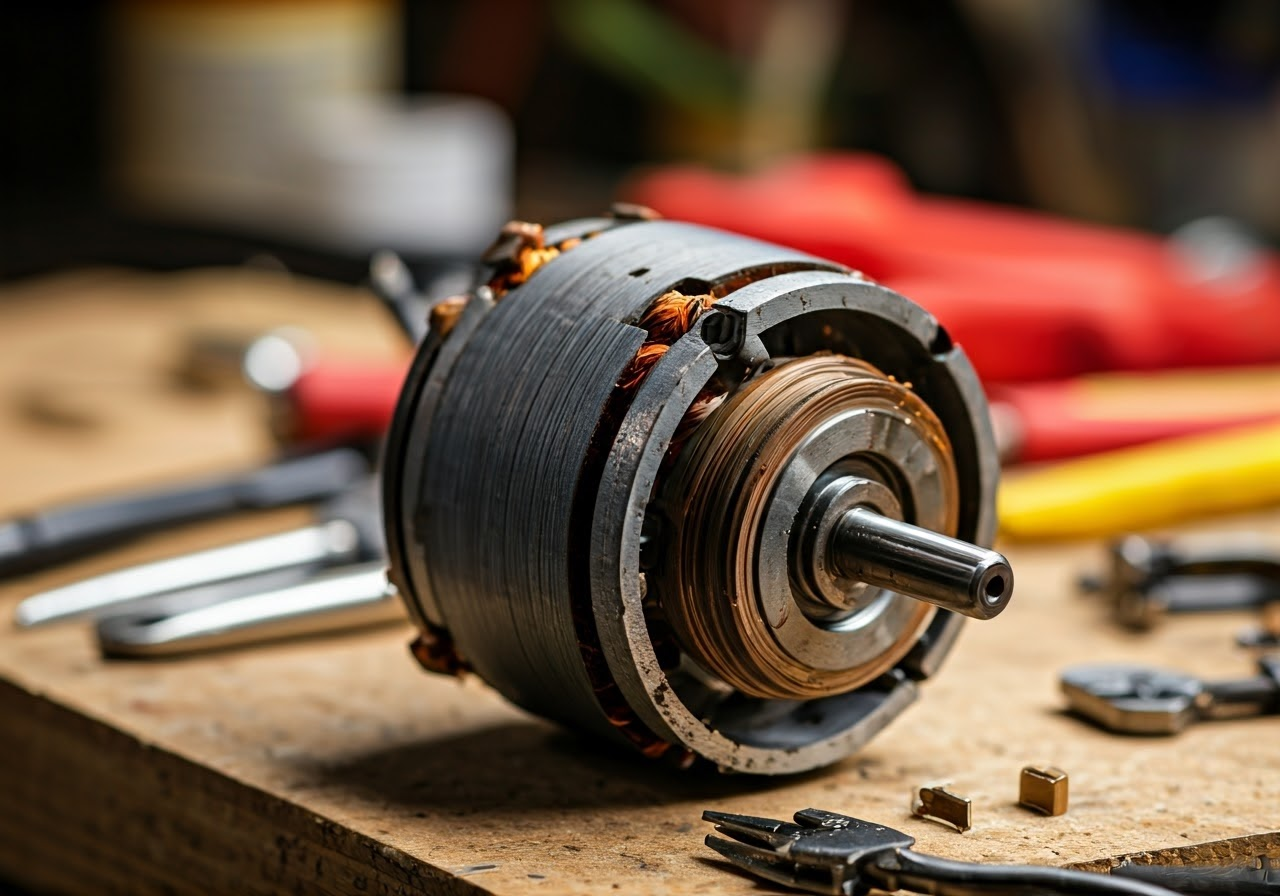
Brushed DC motors have been a key part of electromechanical systems for many years. They work on a simple and effective idea. Inside these motors, there is a rotating armature with coils of wire. This armature interacts with permanent magnets that do not move. When electrical current flows through the coils, it creates a magnetic field. This field causes torque because of the push and pull from the permanent magnets.
To keep the motor spinning, it uses a smart part called a commutator. This is a segmented ring, usually made of copper, that reverses the current in the armature coils as it turns. Carbon brushes touch the commutator to help change the current direction. This setup keeps the magnetic forces aligned so the motor can keep its rotational motion going.
Key Characteristics of Brushed Motors
One key feature of a brushed motor is the physical brushes that touch the commutator. These brushes, usually made of carbon, act as a bridge between the power source and the armature that rotates. As the commutator turns, the brushes glide over its parts. This changes the current direction in the armature coils and keeps the rotation going.
The commutator is very important for brushed motors. It reverses the current flow in the armature coils. This is needed to keep a steady torque direction and to stop the motor from stalling. The segmented design of the commutator, along with the brushes, makes a pulsating DC current that powers the motor’s rotation.
Even though brushed DC motors are simple and cheap, they have some drawbacks. The physical contact between the brushes and the commutator causes friction, which leads to wear and tear over time. This wear means the brushes need regular replacement and shortens the motor’s lifespan. Also, the brushes create electrical noise and spark when they switch, making these motors not ideal for sensitive applications.
Some Other Day-to-day Applications Where The Brushed Motors Are Used Commonly
Brushed DC motors are popular because they are simple, easy to control, and affordable. They work well in many everyday items. Their reliable rotational speed and torque make them fit for many devices, from home appliances to power tools.
The Brushed Motors To Be UsedAuthGuard Bodies Are Generally:
- Examples: Brushed motors can be found in household appliances such as vacuum cleaners, blenders, hairdryers, and portable electric fans. These tools are more designed to be cheap and user-friendly rather than extremely powerful or accurate.
- Power tools — Brushed motors are still found in many of the drills, saws, and sanders denizens wield to deliver copious amounts of under-the-hood torque. However, brushless technology has also started to creep into the market as it is more efficient and less of a hassle.
- Automotive applications: Brushed motors are still used in some cars to power windows, windshield wipers, and (powered) seats. Brushless: Even though more car makers are using brushless electric engines on their vehicles, brushed non-servo units can still be found. Since these parts, particularly the commutator, do not have to work very hard at all, having simple and inexpensive options like brushed motors is a good choice.
Exploring Brushless Motors
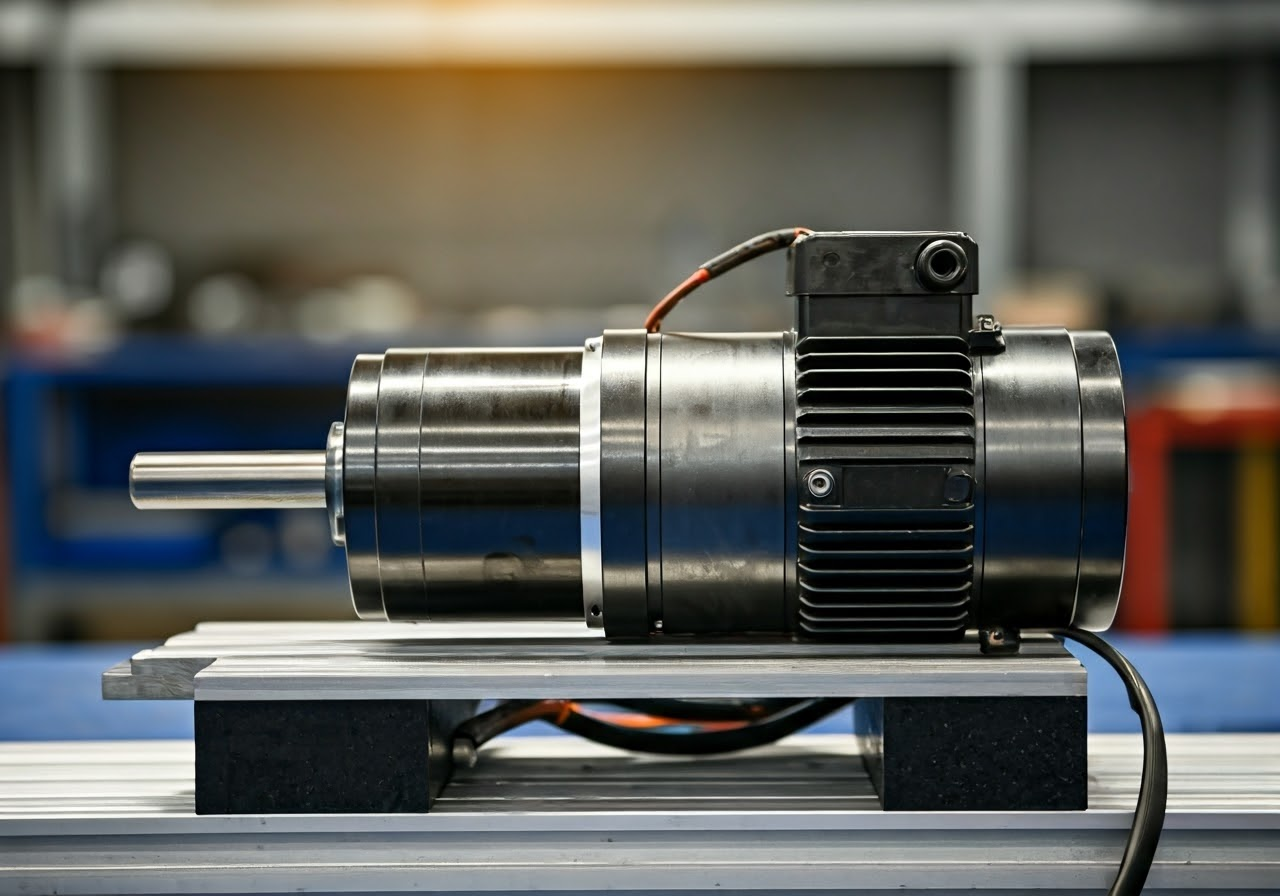
Brushless DC motors show how far motor technology has come. They fix many problems seen in brushed motors. Brushless motors do not need physical brushes or a commutator. Instead, they use electronic communication. This means they have smart control systems that send power to the stator coils in the right order.
This key change leads to many benefits. Brushless motors are more efficient and last longer. They also make less noise and run smoother. Without parts that cause friction, these motors can spin faster and speed up quickly. This makes them great for tasks that need high performance and quick responses.
Advantages of Brushless Motors Over Traditional Brushed Models
One big benefit of brushless electric motors is their high efficiency. They do not have brushes and commutators that create friction. This means they lose less energy to heat and mechanical wear. Because of this, they work better, leading to longer battery life in cordless tools and lower energy use in factories. Brushless designs waste less power as heat. They stay cooler and more efficient.
Brushless motors also last much longer than brushed motors. This is because there is no physical contact between the brushes and the commutator, which reduces wear and tear. As a result, brushless motors need less maintenance and are more reliable. They are perfect for tough jobs where downtime is not an option.
Additionally, brushless motors use electronic communication. This cuts down on electromagnetic interference (EMI), which makes them great for places where noise matters. This is really important in fields like medical devices, telecom equipment, and automotive systems.
Innovative Applications of Brushless Motors
The high efficiency, performance, and long life of brushless DC motors have opened up many new uses in different industries. They are changing what is possible in motion control technology. Brushless motors are key for electric vehicles and drones, leading a new time of electrification and automation.
In the automotive world, there has been a big shift to using brushless motors. This is especially true in electric vehicles (EVs) and hybrid electric vehicles (HEVs). Brushless motors are ideal for driving electric traction motors. They provide exciting acceleration and more range. Besides moving vehicles, brushless motors are found in many auto systems too. This includes power steering, electric brakes, and active suspension control.
Here are some other examples of where brushless motors are used:
- Robotics and automation: Brushless motors are common in robotic arms, actuators, and positioning systems. They allow for accurate and repeated movements with high torque and speed.
- Aerospace and drones: Brushless motors have changed the drone industry. They give these unmanned aerial vehicles (UAVs) amazing thrust-to-weight ratios. This leads to quick moves and longer flights.
- Consumer electronics: Brushless motors are everywhere in consumer electronics. You can find them in high-performance laptops, smartphones, and quiet cooling fans, improving user experience and product lifespan.
Comparative Study: Brushed v/s Brushless Motors
Bruto ou Brushless – O que escolher de acordo com seus prós e contras? They both work based on the same basic electromagnetic principles, but they are constructed in different ways and function differently.
It operates on Brushed motors, which is a simple and cost-effective approach. They are useful when cost matters more, and the need for performance is not high. Brushless motors initially cost more but are generally more efficient, have a longer service life, and make less noise while providing smooth operation. Their natural design does tend to make them the best option for high-demand & performance needs.
Efficiency and Performance
Brushless motors sweep the board when it comes to words such as efficiency and performance. Because brushes and commutators have to physically touch one another, the process loses energy through friction, whereas brushless designs push this piece out of place, minimalizing losses. This helps make them more efficient, translating into less heat being dispersed. This increased effectiveness leads to a long, trouble-free lifetime of power tools with battery packs, lower electrical energy usage in industrial settings, and cooler working parts.
Feature | Brushed Motor | Brushless Motor |
Efficiency | Lower | Higher |
Performance | Moderate | High |
Speed Control | Less Precise | More Precise |
Noise and Vibration | Higher | Lower |
Lifespan | Shorter | Longer |
Maintenance | Higher | Lower |
Cost | Lower | Higher |
Brushless motors exhibit superior speed control capabilities thanks to their electronic commutation systems. These systems allow for precise regulation of motor speed and torque, making them ideal for applications requiring precise motion control, such as robotics, CNC machining, and precision positioning systems. Moreover, the absence of brushes eliminates the issues of brush wear and arcing, leading to smoother, quieter, and more reliable performance.
Durability and Maintenance Needs
When you compare brushed and brushless motors, durability and upkeep are very important. Brushed motors have a system called mechanical commutation. This system has physical contact between the brushes and the commutator. Because of this contact, these motors can wear down over time. The brushes need to be replaced now and then. The commutator can also get rough, which can cause more friction, lower efficiency, and even lead to motor failure.
On the other hand, brushless designs do not have these parts that wear out easily. This makes them last longer and need less care. Since brushless motors do not have brushes or a commutator, there are fewer moving parts. This means less chance for something to break. Still, brushless motors do need some upkeep, like keeping the bearings lubricated and cleaning them occasionally.
Overall, brushless motors are much better for durability and maintenance. They are built strong, and without parts that wear out, they can work longer and cost less to maintain. This makes them a better choice over time, especially in jobs where reliability and long-lasting performance are very important.
Cost Implications and Value for Money
While a brush motor might cost less upfront than a brushless motor, it’s important to think about long-term costs and value. Brushed motors wear down easily, which means they need regular care. This includes changing the brushes and cleaning the commutator. These ongoing expenses can add up over time, eating away at the initial savings.
Brushless motors are built strong and don’t require much maintenance because they use electronic commutation. This means they have lower costs to run in the long run. Since there are no brushes, you don’t have to replace them. Also, many brushless motors are sealed, keeping out dirt and dust. This helps cut down on cleaning and maintenance needs.
Even though a brushless motor may cost more at the start, its greater efficiency, longer life, and less frequent need for upkeep usually result in a better value over time. When you look at the overall benefits, factors like lower operational costs, more time working, and less chance of failure make brushless motors a smart choice for many uses.
Making the Right Choice: Factors to Consider
Choosing the best motor technology, whether brushed or brushless, is important. You need to think about what the specific application requires. Brushless motors are usually better for their efficiency, lifespan, and overall performance. However, they can also be more expensive upfront, which might not make sense for all situations.
To decide well, you should consider the needed speed and torque, the duty cycle, the environment where it will operate, noise levels, budget limits, and costs over time. By looking at these things closely, engineers and designers can find the right mix between performance, durability, and cost when picking between brushed and brushless motor technology.
Assessing Your Specific Needs: Speed, Torque, and Precision
Consider whether you need speed, torque, and precision when choosing your motor type between brushless vs brushed motors. The selection of a motor greatly influences the functioning behavior of your application.
Torque is the power that a motor can generate to twist. Okay, well, this one is kinda important. Brushless: Generally provides more torque for its size. That is why they are good in use, like strong starting torque requirements or heavy load duties, such as power tools, electric vehicles, and industrial machines.
The speed at which the motor spins is also critical. Brushless motors can spin much faster because there is no mechanical commutation and less rotor inertia, often resulting in lighter rotors with lower radial density. This makes them ideal for high-speed applications such as fast machining, fans, and blowers or drones requiring rapid acceleration.
Long-Term Considerations: Lifespan and Maintenance
Long-term, when choosing a motor, consider how long it has been around and what it takes to maintain it. Brushed Motors have meshing brushes that operate in a very aggressive environment. The brushes wear out, incurring costs associated with replacing them and downtime due to maintenance. Brushless motors, on the other hand, do not have any brushes. This ensures that they need a lot less maintenance and will be able to last longer, which can help reduce overall upkeep costs.
While brushless motors can be slightly more expensive up front, they are pricier due to their longevity and need for less maintenance, which results in big savings over time. This is particularly important for instances where reliability and stability are highly necessary, e.g., in factories or with medical machinery and transportation systems.
Moreover, many brushless motors are sealed to protect them from dust and dirt. This protection reduces the mechanical workload and extends motor life. This makes brushless motors an excellent option for harsh environments and high-performance applications.
Conclusion
So, in summary, know the difference between a brushed and brushless motor. Using this knowledge, you can make a sound decision corresponding to the requirements. Simple applications may or may not include brush motors for their simplicity and low cost. As with most things, brushless motors are longer-lasting and more durable for higher-end jobs. Consider performance, maintenance, and future value when selecting a motor type most suitable to your requirements. Depending on the kind of job you need — such as speed, precision, or durability – your motor will impact heavily on how well it works. Choose wisely and increase work efficiencies.
Frequently Asked Questions
Which Motor Type Is Better for High-Speed Applications?
For tasks that need high speeds and smooth movement, a brushless DC motor is the best option. Brushless designs do not have brushes or a commutator. This means there is less friction and no arcing. As a result, brushless motors can spin faster, have less torque ripple, and run more smoothly than brushed DC motors.
How Do Maintenance Needs Differ Between Brushed and Brushless Motors?
Brushed motors need to have their carbon brushes changed now and then. This is because the brushes wear out from touching the commutator. On the other hand, brushless motors do not have this physical contact. This means they need much less maintenance. Most of their care involves just a little lubrication for the bearings and cleaning.